- Ball Valves
- Flanged Floating Ball Valve
- Trunnion Mounted Ball Valves
- Threaded Ball Valves
- Welded End Ball Valves
- Gate Valves
- Flanged Gate Valves
- Welded Gate Valves
- Threaded Gate Valves
- Globe Valves
- Flanged Globe Valves
- Weld End Globe Valves
- Threaded Globe Valves
- Check Valves
- Flanged Check Valves
- Welded Ends Check Valves
- Threaded Check Valves
- Y Type Strainers
- Flanged Y Type Strainers
- Threaded Y Type Strainers
- Forged Steel Valves
- Flanged Forged Steel Valves
- Threaded Forged Steel Valves
- Threaded Forged Steel Gate Valve
- Threaded Forged Steel Globe Valve
- Threaded Forged Steel Check Valve
- Threaded Forged Steel Y Type Strainer
- Welded Ends Forged Steel Valves
Threaded Forged Steel Globe Valve
Description
Threaded forged steel globe valve is a valve with closure member (disc) moving along with the center line with valve seat. It is mainly composed of valve body, disc, shaft pin and stem. The stem axis of this threaded globe valve is vertical to sealing surface of valve seat. With short opening and closing stroke and reliable cutting off performance, this forged steel valve is widely used for cutting off and regulating medium flow.
Application
Our threaded forged steel globe valve is widely applied on tap water, sewage, building, petroleum, chemical, food, medicine, textile, electricity, ship, metallurgy, energy and other pipeline systems.
Advantages of Threaded Globe Valve
1. Globe valve is much easier than gate valve in structure, manufacturing and maintenance.
2. It needs small torsion to open the forged steel valve.
3. Threaded forged steel globe valve is featured by fine sealing performance and long service time.
4. Friction is small between sealing surfaces.
5. All our products have passed CE and JB/T9092 certification.
6. 18 months warranty and lifetime technology service are offered for our products.
Features
1. Precision casting technology is adopted to manufacture valve body.
2. Two times shot blasting makes exquisite outward appearance of the threaded globe valve.
3. CNC processing is applied on valve disc.
4. When opened or closed, there is no relative sliding between valve body and disc.
5. Globe valve is lower but longer than gate valve.
6. Since medium channel twists and turns in valve body, the fluid resistance is big.
7. The medium in threaded forged steel globe valve can only flow in one direction and the flowing direction can not be changed when the forged steel valve is in operation.
8. The disc often endures erosion when fully opened.
Classifications of Threaded Globe Valve
1. According to channel direction of globe valve, it can be classified into straight through type/straight flow type/angle type/plunger type globe valve.
2. According to the location of the thread on valve stem, it can be divided into upper/lower threaded stem globe valve.
3. According to application, it can be classified into heating jacket/forged steel/oxygen dedicated/bellows/low temperature globe valve (stop valve).
Pressure: CLASS900-1500 PN16.0~26.0
1. Bolted Bonnet/Welded Bonnet Pressure Sealed Bonnet
2. Full Port
3. General or Needle Type Disc
4. Treaded Ends or SW Ends
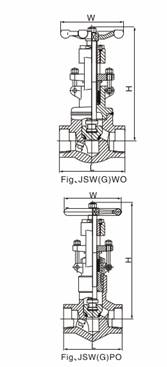
Technical Specification of Threaded Globe Valve
Technical Specification | ASME/API/BS | GB/JB |
Design Standard | BS5352 | GB/T7746 |
Pressure-Temperature Rating | ASME B16.34 | GB/T12224 |
Face-Face | Factory Standard | GB/T7746 |
Socket-Welded Ends | ASME B16.11 | GB/T1751 |
Threaded Ends | ASME B1.20.1 | GB/T306 |
Inspection & Test | API598 | JB/T9092 |
Material List for Main Parts of Threaded Globe Valve
No. | Part Name | ASTM | |||
Carbon Steel | Tailess Steel | Alloy Steel | |||
1 | Body | A105 | LF2/LF3 | A182 F304 | A182 F11/F22 |
2 | Disc | A182F6a | A182F6a | A182 F304 | A182 F6a |
3 | Stem | A276-410 | A276-410 | A276-304 | A276-410 |
4 | Gasket | Graphite+304 | |||
5 | Sealing Ring | Graphite | |||
6 | Yoke | A216-WCB | A216-WCB | A351 CF8 | A216-WCB |
7 | Bonnet | A105 | LF2/LF3 | A182 F304 | A182 F11/F22 |
8 | Gland | A216-WCB | A216-WCB | A351 CF8 | A216-WCB |
9 | Bolt | A193 B7 | A320L7 | A193 B8 | A193 B16 |
10 | Packing | Graphite | |||
11 | Stem Bushing | A276-410 | A276-410 | A276-304 | A276-410 |
12 | Gland | A216-WCB | A216-WCB | A351 CF8 | A216-WCB |
13 | Eye Blot | A193 B7 | A320 L7 | A193 B8 | A193 B7 |
14 | Stem Nut | A276-410 | |||
15 | Handwheel | A197 or A47-32510 |
Main Dimensions & Weight of Threaded Globe Valve
Pressure | Size | Main Dimension of Forged Steel Valve | Weight(kg) | |||||||||
mm | in. | D | L | H | W | |||||||
BB/WB | PB | BB/WB | PB | BB/WB | PB | BB/WB | PB | WB | PB | |||
CLASS900 PN16.0 | 8 | 1/4 | 7 | - | 111 | - | 207 | - | 100 | - | 2.4 | - |
10 | 3/8 | 10 | - | 111 | - | 207 | - | 100 | - | 2.2 | - | |
15 | 1/2 | 13 | 13 | 111 | 140 | 207 | 207 | 100 | 125 | 2.0 | 11.2 | |
20 | 3/4 | 18 | 18 | 130 | 140 | 240 | 207 | 125 | 125 | 3.8 | 10.5 | |
25 | 1 | 24 | 24 | 152 | 140 | 258 | 240 | 160 | 160 | 4.2 | 10.1 | |
32 | 1-1/4 | 29 | 29 | 172 | 178 | 290 | 258 | 160 | 160 | 8.0 | 21.0 | |
40 | 1-1/2 | 36.5 | 36.5 | 220 | 178 | 337 | 290 | 180 | 180 | 13.2 | 19.6 | |
50 | 2 | 46.5 | 46.5 | 235 | 216 | 354 | 337 | 240 | 240 | 16.8 | 40.4 | |
CLASS1500 PN26.0 | 8 | 1/4 | 7 | - | 111 | - | 207 | - | 100 | - | 2.4 | - |
10 | 3/8 | 10 | - | 111 | - | 207 | - | 100 | - | 2.2 | - | |
15 | 1/2 | 13 | 13 | 111 | 140 | 207 | 207 | 100 | 125 | 2.0 | 11.2 | |
20 | 3/4 | 18 | 18 | 130 | 140 | 240 | 207 | 125 | 125 | 3.8 | 10.5 | |
25 | 1 | 24 | 24 | 152 | 140 | 258 | 240 | 160 | 160 | 4.2 | 10.1 | |
32 | 1-1/4 | 29 | 29 | 172 | 178 | 290 | 258 | 160 | 160 | 8.0 | 21.0 | |
40 | 1-1/2 | 36.5 | 36.5 | 220 | 178 | 337 | 290 | 180 | 180 | 13.2 | 19.6 | |
50 | 2 | 46.5 | 46.5 | 235 | 216 | 354 | 337 | 240 | 240 | 16.8 | 40.4 |
Possible Malfunction, Reason and Solution
Possible Malfunction | Reason | Solution |
Leakage Between Disc and Valve Seat Sealing Surface | 1.Dirty Stuff Attachment on Sealing Surface 2.Wear or Erosion of Sealing Surface 3.Deformation of Disc Caused by Excessive Closing Torsion | 1.Cleaning Dirty Stuff 2.Regrinding Sealing Surface for Surfacing and Processing 3.Replacing the Forged Steel Valve |
Leakage Between Bolted Bonnet Valve Body and Bonnet Joint | 1.Uneven Fastening of Connection Studs 2.Damage on Sealing Surface 3.Wear or Invalidity of Gasket | 1.Refastening Evenly 2.Repairing 3.Repalcing Gasket |
Leakage at Valve Stem Packing Position | 1.Malcompression of Packing Grand 2.Wear of the Packing 3.Damage of Contact Surface between the Stem and Packing | 1.Tightening Compression Packing Gland Nut Evenly 2.Increasing Packing Properly 3.Grinding Stem Surface or Replacing Stem |
Inflexible Falling and Rising of Valve Stem | 1.Too Tight Packing Gland 2.Skewing Packing Gland 3.Clutter in Rotating Parts 4.Damage on Stem and Thread of Valve Stem Nut 5.Stem Bending | 1.Appropriate Release of Packing Grand 2.Adjusting Packing Gland 3.Removing Clutters and Coating Lubricating Grease 4.Truing Thread or Replacing Stem and Valve Stem Nut 5.Adjusting or Replacing Valve Stem |
- Threaded Forged Steel Check ValveThreaded forged steel check valve, also called non return valve, reflux valve, one-way valve or counterbalance valve, is mainly made up of valve body, disc, bonnet and gasket. It is used to prevent back flow and leakage of medium as well as inversion of pump and driving motor. By relying on media flow to open and close disc automatically. It can also be installed on ...